Poki Machine
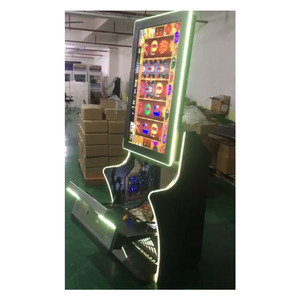
Squish Machine is a skill game where you have to make your way through the level before the machine gets to you. Not only do you have to make your way to the finish button in. Finn's Fantastic Food Machine is a fast-paced restaurant game created by Light Wolf Studios. Collect plates as they come out of the kitchen and make sure they get delivered to the right table! If you've always wondered what it would be like to work in a chaotic restaurant, Finn's Fantastic Food Machine. Description: Play a Machine Gun Squad online at Friv-Poki.com. Machine Gun Squad belongs to the Fighting Games category. In Fighting Games, we have a similar collection of games with Machine Gun Squad.You can play all of our games at Friv Poki games. Machine Gun Squad is a very fun game that you can play with other people around the world. Why should I play the Buffalo slot machine? Buffalo is one of the most popular free slots out there, and is an all-time favorite for many players. The game is part of Ainsworth’s XTRA Reel Power series, which means you have up to 1024 ways to win.
Poka-yoke (ポカヨケ, [poka joke]) is a Japanese term that means 'mistake-proofing' or 'inadvertent error prevention'. A poka-yoke is any mechanism in a process that helps an equipment operator avoid (yokeru) mistakes (poka) defects by preventing, correcting, or drawing attention to human errors as they occur.[1] The concept was formalized, and the term adopted, by Shigeo Shingo as part of the Toyota Production System.[2][3]
Etymology[edit]
Poka-yoke was originally baka-yoke, but as this means 'fool-proofing' (or 'idiot-proofing') the name was changed to the milder poka-yoke.[citation needed]Poka-yoke is derived from poka o yokeru (ポカを除ける), a term in shogi and igo referring to avoiding an unthinkably bad move.
Usage[edit]
More broadly, the term can refer to any behavior-shaping constraint designed into a process to prevent incorrect operation by the user.
A simple poka-yoke example is demonstrated when a driver of the car equipped with a manual gearbox must press on the clutch pedal (a process step, therefore a poka-yoke) prior to starting an automobile. The interlock serves to prevent unintended movement of the car. Another example of poka-yoke would be the car equipped with an automatic transmission, which has a switch that requires the car to be in 'Park' or 'Neutral' before the car can be started (some automatic transmissions require the brake pedal to be depressed as well). These serve as behavior-shaping constraints as the action of 'car in Park (or Neutral)' or 'foot depressing the clutch/brake pedal' must be performed before the car is allowed to start. The requirement of a depressed brake pedal to shift most of the cars with an automatic transmission from 'Park' to any other gear is yet another example of a poka-yoke application. Over time, the driver's behavior is conformed with the requirements by repetition and habit.
History[edit]
The term poka-yoke was applied by Shigeo Shingo in the 1960s to industrial processes designed to prevent human errors.[4] Shingo redesigned a process in which factory workers, while assembling a small switch, would often forget to insert the required spring under one of the switch buttons. In the redesigned process, the worker would perform the task in two steps, first preparing the two required springs and placing them in a placeholder, then inserting the springs from the placeholder into the switch. When a spring remained in the placeholder, the workers knew that they had forgotten to insert it and could correct the mistake effortlessly.[5]
Shingo distinguished between the concepts of inevitable human mistakes and defects in the production. Defects occur when the mistakes are allowed to reach the customer. The aim of poka-yoke is to design the process so that mistakes can be detected and corrected immediately, eliminating defects at the source.
Implementation in manufacturing[edit]
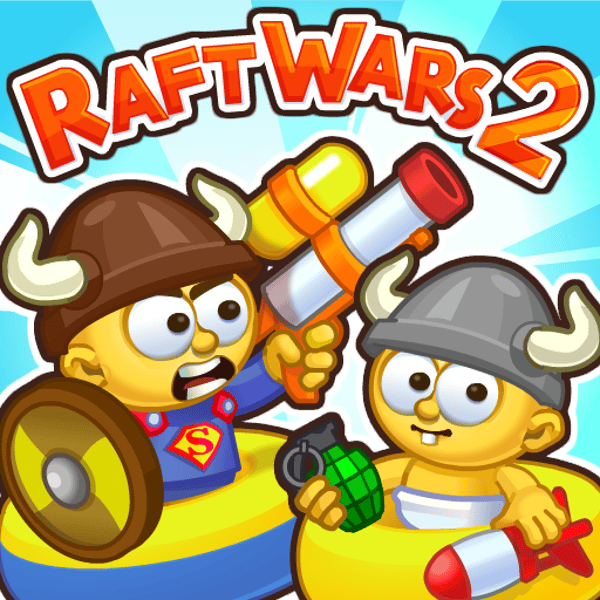
Poka-yoke can be implemented at any step of a manufacturing process where something can go wrong or an error can be made.[6] For example, a fixture that holds pieces for processing might be modified to only allow pieces to be held in the correct orientation,[7] or a digital counter might track the number of spot welds on each piece to ensure that the worker executes the correct number of welds.[7]
Shigeo Shingo recognized three types of poka-yoke for detecting and preventing errors in a mass production system:[2][6]
- The contact method identifies product defects by testing the product's shape, size, color, or other physical attributes.
- The fixed-value (or constant number) method alerts the operator if a certain number of movements are not made.
- The motion-step (or sequence) method determines whether the prescribed steps of the process have been followed.
Either the operator is alerted when a mistake is about to be made, or the poka-yoke device actually prevents the mistake from being made. In Shingo's lexicon, the former implementation would be called a warning poka-yoke, while the latter would be referred to as a control poka-yoke.[2]
Shingo argued that errors are inevitable in any manufacturing process, but that if appropriate poka-yokes are implemented, then mistakes can be caught quickly and prevented from resulting in defects. By eliminating defects at the source, the cost of mistakes within a company is reduced.[citation needed]
A methodic approach to build up poka-yoke countermeasures has been proposed by the Applied Problem Solving (APS) methodology,[8] which consists of a three-step analysis of the risks to be managed:
- Identification of the need
- Identification of possible mistakes
- Management of mistakes before satisfying the need
This approach can be used to emphasize the technical aspect of finding effective solutions during brainstorming sessions.
Benefits of poka-yoke implementation[edit]
A typical feature of poka-yoke solutions is that they don't let an error in a process happen. Other advantages include:[9]
- Less time spent on training workers;
- Elimination of many operations related to quality control;
- Unburdening of operators from repetitive operations;
- Promotion of the work improvement-oriented approach and actions;
- A reduced number of rejects;
- Immediate action when a problem occurs;
- 100% built-in quality control;
- Preventing bad products from reaching customers;
- Detecting mistakes as they occur;
- Eliminating defects before they occur.
See also[edit]
References[edit]
- ^Robinson, Harry (1997). 'Using Poka-Yoke Techniques for Early Defect Detection'. Archived from the original on December 27, 2014. Retrieved May 4, 2009.
- ^ abcShingo, Shigeo; Dillon, Andrew (1989). A study of the Toyota production system from an industrial engineering viewpoint. Portland, OR: Productivity Press. ISBN0-915299-17-8. OCLC19740349.
- ^John R. Grout, Brian T. Downs. 'A Brief Tutorial on Mistake-proofing, Poka-Yoke, and ZQC'. MistakeProofing.com. Retrieved May 4, 2009.
- ^H Robinson. 'Using Poka-Yoke techniques for early defect detection'. Archived from the original on December 27, 2014. Retrieved June 18, 2012.
- ^'The Sayings of Shigeo Shingo: Key Strategies for Plant Improvement'. QualityCoach.Net. Archived from the original on January 28, 2014. Retrieved August 20, 2012.
- ^ ab'Poka Yoke or Mistake Proofing :: Overview'. The Quality Portal. Retrieved May 5, 2009.
- ^ abNikkan Kogyo Shimbun (1988). Poka-yoke: improving product quality by preventing defects. Productivity Press. p. 111. ISBN978-0-915299-31-7.
- ^Ivan Fantin (2014). Applied Problem Solving. Method, Applications, Root Causes, Countermeasures, Poka-Yoke and A3. How to make things happen to solve problems. Milan, Italy: Createspace, an Amazon company. ISBN978-1499122282
- ^Misiurek, Bartosz (2016). Standardized Work with TWI: Eliminating Human Errors in Production and Service Processes. New York: Productivity Press. ISBN9781498737548.
Further reading[edit]
Free Pokie Slots No Download
- Shingo, Shigeo (1986). Zero quality control: source inspection and the poka-yoke system. Portland, Oregon: Productivity Press. ISBN0-915299-07-0. OCLC13457086. Retrieved 30 April 2009.
- Nikkan Kogyo Shimbun (1988). Poka-yoke: improving product quality by preventing defects. Portland, Oregon: Productivity Press. ISBN0-915299-31-3. OCLC300302752.
- Hinckley, C. M.; P. Barkan (1995). 'The role of variation, mistakes, and complexity in producing nonconformities'. Journal of Quality Technology. 27 (3): 242–249. doi:10.1080/00224065.1995.11979596.
- Misiurek, Bartosz (2016). Standardized Work with TWI: Eliminating Human Errors in Production and Service Processes. New York: Productivity Press. ISBN9781498737548.